Posting Rules | post new threads post replies post attachments edit your posts is are code is are are are | Similar Threads | Thread | Thread Starter | Forum | Replies | Last Post | | Chotu | Multihull Sailboats | 176 | 08-08-2022 06:29 | | mlydon | Deck hardware: Rigging, Sails & Hoisting | 6 | 17-02-2019 06:44 | | Eastward ho 24 | Deck hardware: Rigging, Sails & Hoisting | 33 | 24-01-2018 19:50 | | montenido | Monohull Sailboats | 4 | 08-05-2012 18:55 | | blahman | Deck hardware: Rigging, Sails & Hoisting | 33 | 07-11-2011 08:46 | Privacy Guaranteed - your email is never shared with anyone, opt out any time. - New Sailboats
- Sailboats 21-30ft
- Sailboats 31-35ft
- Sailboats 36-40ft
- Sailboats Over 40ft
- Sailboats Under 21feet
- used_sailboats
- Apps and Computer Programs
- Communications
- Fishfinders
- Handheld Electronics
- Plotters MFDS Rradar
- Wind, Speed & Depth Instruments
- Anchoring Mooring
- Running Rigging
- Sails Canvas
- Standing Rigging
- Diesel Engines
- Off Grid Energy
- Cleaning Waxing
- DIY Projects
- Repair, Tools & Materials
- Spare Parts
- Tools & Gadgets
- Cabin Comfort
- Ventilation
- Footwear Apparel
- Foul Weather Gear
- Mailport & PS Advisor
- Inside Practical Sailor Blog
- Activate My Web Access
- Reset Password
- Customer Service
  The PDQ 32 Cruising Cat Used Boat Review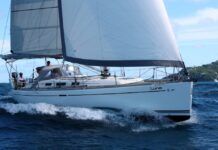 Dufour 44 Used Boat Review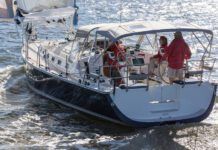 Blue Jacket 40 Used Boat Review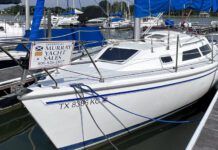 Catalina 270 vs. The Beneteau First 265 Used Boat Match-Up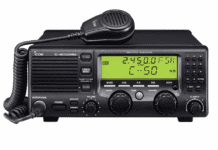 How to Create a Bullet-Proof VHF/SSB Backup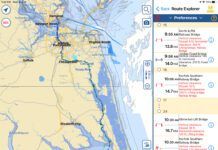 Tips From A First “Sail” on the ICW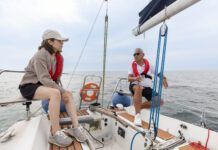 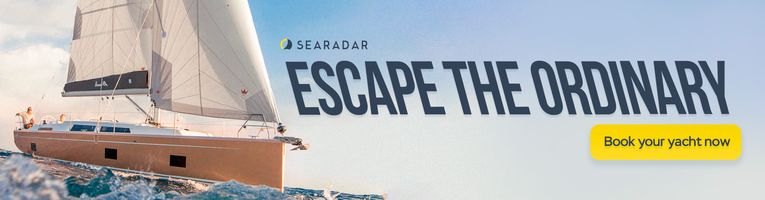 Tillerpilot Tips and Safety Cautions Best Crimpers and Strippers for Fixing Marine Electrical Connectors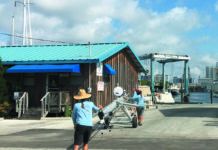 Revive Your Mast Like a Pro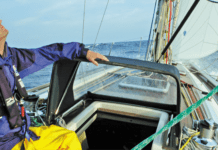 Solving the Dodger Dilemma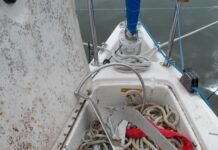 Polyester vs. Nylon Rode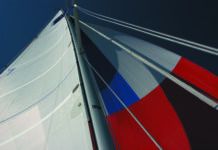 Getting the Most Out of Older Sails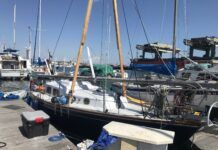 Sailing Triteia: Budget Bluewater Cruising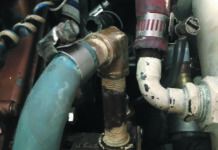 How To Keep Pipe Fittings Dry: Sealant and Teflon Tape Tests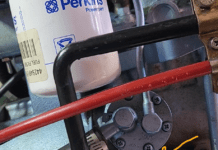 Fuel Lift Pump: Easy DIY Diesel Fuel System Diagnostic and Repair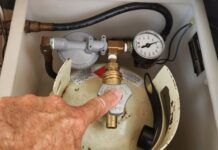 Propane Leak: How to Detect, Locate and Fix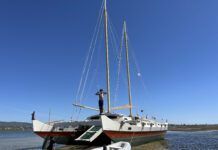 Why Choose the Wharram Design?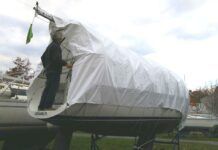 Winterizing: Make It Easy With Checklists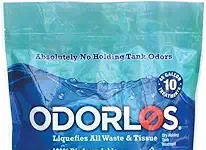 Stopping Holding-tank Odors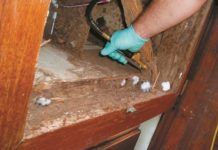 Giving Bugs the Big Goodbye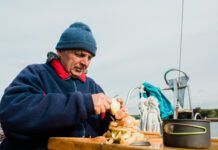 Galley Gadgets for the Cruising Sailor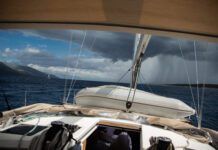 The Rain Catcher’s Guide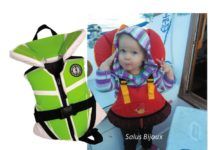 Sailing Gear for Kids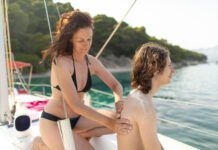 What’s the Best Sunscreen?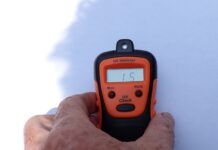 UV Clothing: Is It Worth the Hype? Preparing Yourself for Solo Sailing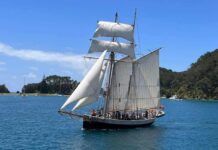 R. Tucker Thompson Tall Ship Youth Voyage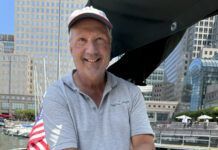 On Watch: This 60-Year-Old Hinckley Pilot 35 is Also a Working…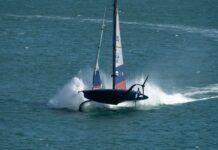 On Watch: America’s Cup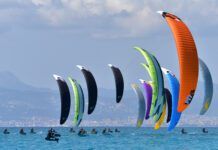 On Watch: All Eyes on Europe Sail Racing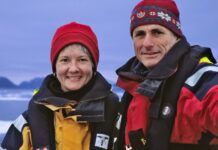 Dear Readers- Sails, Rigging & Deck Gear
Chainplates RevisitedChainplate failures aren't common, but when one occurred on a new boat during its inaugural sailwith our reviewer aboardwe knew it was time to investigate. here's the result of our initial probing.. 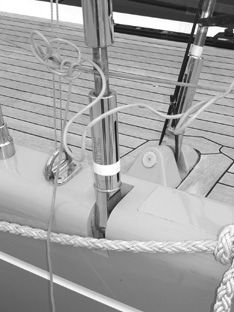 Following our review of the new J/133 (PS Oct. 1, ’04), in which we recounted a chainplate failure aboard hull No. 3 on its maiden voyage, a reader’s letter prompted us to review the manner in which manufacturers design and construct the critical connections between mast, shrouds, and a boat’s structure. In the case of the J/133, we concluded that the construction method—a contemporary yet time-tested approach—was properly conceived, but poorly executed. The folks at J/Boats declined to offer specific comments, but the boat’s builder—Pearson Composites, LLC (formerly TPI)—told us that ours was a fair assessment of the situation. (More on that later.) Nonetheless, the issue of chainplate construction and rig attachment demands further examination, particularly for the owners of older boats whose vessels may be susceptible to chainplate failure. Like the human anatomy, which is supported by a series of bones connected at joints (“head bone connected to the neck bone, neck bone connected to the shoulder bone”), a sailboat’s standing rigging reflects many similar connections. At one end of any stayed rig, the head of the mast is supported by stays and shrouds that in most cases disappear belowdecks to connect to a metal, wood, or fiberglass section that itself is attached to a bulkhead, the hull’s topsides or bottom, or an interior grid system. With any rig, contrary forces are at work. At the masthead, tensioned shrouds pulling chainplates upward from a grid in the bottom of the hull, for instance, are at the same time pushing the butt of the mast, or a compression post, in the opposite direction. Consider that the headstay and backstay are pulling the bow and stern upward, and the conflicting forces on the entire structure are enormous. “The static pressure on the hull of the Santa Cruz 70 produced by the mast, with the boat sitting static at a dock, is approximately 28,000 pounds,” explained Lance Brown, president of Santa Cruz Yachts. Given that, it’s no surprise that America’s Cup boats, which take advantage of every weight-saving method available, often have major failures. Creating a proper set of connectors, then, requires that designer, engineer, boatbuilder, and rigging specialist each scientifically calculate the loads that will act on the sails in wind and sea, and the loadbearing capacity of the standing rigging, which will ultimately determine the lamination schedule for chainplates or the appropriate strength characteristics of whatever material is used to fabricate these critical connectors. Ty Goss, of the custom sales division at Navtec, told us that “Once the loads on rigging and turnbuckles are determined, our prototypes are tested by running fatigue tests. “We will load a turnbuckle to its breaking strength and stress it 120,000 to 200,000 times (1.4 times its projected life expectancy) in 15-second cycles. If it doesn’t break, we know we have the right product.” On older boats, chainplates were often fashioned from necessary, but unsightly, metal straps attached to the exterior. Unless an owner diligently polished them, the straps or their fittings typically rusted, which produced blemishes on the topsides. These same rust lines, however, could provide an owner with visible evidence of the potential deterioration of the plates, or their fasteners. On modern fiberglass boats, chainplates are usually out of sight and out of mind. As builders became more confident of the bonding capacity and strength of fiberglass, they began relocating these straps on the hull’s inner skin, or bedded in bulkheads. However, as with the exterior attachments, the new method was not without its drawbacks, since a leak at deck level could result in delamination of the fiberglass, or a waterfilled core; either condition reducing the structural integrity of the components. Various methods of attaching plates are used, including the method employed by Pearson Composites, LLC in the construction of the new J/133. In that case, the shrouds are connected to a deck plate, which in turn is connected to a tie rod, which is connected to a horizontal pin beddedin a fiberglass buttress in the hull. At PC, LLC, the buttress is a solid fiberglass block with a hole bored that is within 5/1000th” of the size of the pin. This basic design is not new technology; grand-prix racing boats have been employing similar designs for 20 years. The failure of the chainplate on the J/133 was the byproduct of a miscommunication within the builder’s facility, according to Stephen A Misencik, director of engineering and design at PC, LLC. “Miscommunications between engineering and the production floor caused the installation of the deck chainplate assembly to be located 2″ aft of where it was originally designed to be,” Miscencik told us. “This resulted in the tie rod being mis-aligned with both the deck fitting as well as the hull buttress/pinion assembly.” The result: “When the mast and spreaders were constructed by Hall Spars, the shroud-rod connection did not line up properly, placing excessive loads on the fiberglass buttress.” Under sail in 30- to 35-knot winds and a short, steep chop on Lake Michigan, he added “the flange bond on the starboard side on Hull No. 3 failed. Only one edge of the buttress disbonded from the hull.”  When J/Boat’s designers and Misencik compared notes the day after the mishap, the error was discovered, and appropriate modifications completed for future boats. Only one of the five boats that were completed at that time suffered the failure, though a factory team was dispatched to rebuild each of them. Misencik agrees that factory workers could have been alert to a problem when they encountered difficulties installing the misaligned rod during the construction process. Coincidentally, he also describes a problem on some early models of the J/109 that were attributed to the improper use of a bonding material. In that case, chainplates were bonded to a grid framework in the bottom of the hull with ITW Plexus adhesive. “That’s the wrong material to use when trying to produce a rigid structure from two pieces of material,” he explained. The result was excessive flex between the chainplate and the structure. The problem was corrected by replacing the bonding agent with an epoxy mix. Dave Gerr, director of the Westlawn Institute of Marine Technology and a noted yacht designer, told us that the first calculation to be considered in chainplate design is the boat’s righting moment. “Then, the design objective is to take the calculated loads from the shrouds and transmit them to the chainplates, without allowing the deckplate to leak,” he said. “It is important to work out and detail the fastening of the chainplate to the hull because the loads on chainplates are immense,” he added. Designers typically specify standing rigging and attachments, including bolts, that are 1.3 to 1.4 times stronger than the calculated load. This fudge factor is intended to offset the fact that, regardless of the material used, it will degrade over time with aging and a lack of maintenance. “Special considerations, though, relate to the intended use of the boat,” said Santa Cruz Yachts’ Lance Brown. That company’s slogan, “Fast is Fun,” was coined by founder Bill Lee, who built a reputation for designing and constructing rocketships. His legendary Merlin was a record setting 68 footer that introduced “downwind sleds” to the sailing vernacular, and remains the precursor of a breed of boats that have evolved to become the sailing equivalent of a Ferrari. “We built the Santa Cruz 50 and Santa Cruz 70s as race boats, so the interiors were of little consideration, allowing us to place chainplates wherever was necessary to align with the shrouds,” said Brown. Chainplates on the 50-footer were installed using a method mirroring that of the J/133. Shrouds on cruising boats, however, may be located outboard at the rail, for instance, at the expense of tighter sheeting angles and greater pointing ability. And when located outboard, they may be buried behind cabinetry as an aesthetic consideration. “The Santa Cruz 52 (see PS review July 1, ’95), a performance cruiser, is fitted with conventional living and sleeping quarters, so we had to take into consideration the location of seat backs and shelving. We are taking the same approach with the Santa Cruz 53C, which will be introduced in April, 2005.” One conventional method of locating chainplates out of the way is to employ flat metal sections attached to bulkheads with fasteners. “The fastenings,” explained Gerr, “have to be adequately strong, as must the structure they fasten to, in order to distribute the load into the hull. The key to sizing the bolts is to make sure the load from the shroud does not exceed the local crushing strength of the plywood or the laminate that is added to the ply bulkhead to take the chainplate loads. “Elongated chainplate bolt holes in bulkheads are common trouble spots. Without an adequate load bearing area, a bulkhead will eventually crush above the bolt, resulting in the chainplate pulling upward, elongating the bolt holes, and causing the chainplate to leak.” In a worst case scenario, the chainplate may pull through the deck.” To avoid overpopulating a bulkhead with bolts, or using larger bolts, Gerr’s alternative is the installation of an annulus. “They are made of fairly high compressive strength material,” he said, “and increase the bearing area in the ply by making the annulus two times the bolt diameter.” The bolt is then installed through the center of the annulus. On older boats that evidence the potential for this type of failure, an annulus will extend the useful life of the bulkhead with a relatively easy and straightforward fix. Brown describes the forces on chainplates, hull, and mast butt as “contrary forces in a big circle.” To disperse the loads in the new boat from Santa Cruz Yachts, the chainplate will be solid bar stock through-bolted with 12, 1/2″ bolts to a longitudinal stringer that in turn is bonded to the hull and adjoining bulkhead in multiple layers of 0 to 45-degree and 0 to 90-degree fiberglass laid in varied orientations from deck level to the keel. The bulkhead is located on the same reinforced section of the hull as the mast butt, and bonded to the hull and deck. “That structure is so strong that we could cut the center out of the bulkhead without compromising its integrity,” Brown reported. 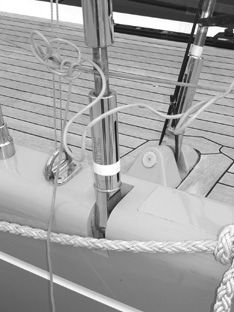 His comment brings to mind a common alternative to the chainplate bulkhead arrangement, which is the construction of a knee (envision an upside-down capital “L”), usually constructed of wood or fiberglass bonded to the hull and under the deck, to which the chainplate is attached. Oriented athwartships, the shape is typically long and narrow so as to accommodate furniture. In this arrangement, the chainlate resembles an inverted “T” shape and is typically cut from a single piece of stainless steel or bronze. Though the knee is tabbed to the hull and deck, Gerr explained, “The knee’s tabbing is secondary bonding, which is structurally rather weak and can suffer from failure due to poor-quality installation, improper resin mixture,” or other factors. For that reason, manufacturers should build in “a large margin of safety,” he said, to ensure a tight structure that will endure hull and deck flex, as well as the worst of the elements. The contemporary method of attaching chainplates involves the replacement of metal straps with tierods that are secured in the hull structure. In this instance, shrouds and rods meet at the center of two plates located on the top and underside of the deck. To produce proper angles at the intersection of the shroud and chainplate, and prevent leaks caused by the deck flexing, builders are employing self-aligning rod caps that reduce the possibility of a failure. At the other end, in many cases the tie rod is attached to the hull or grid in a metal plate into which it is threaded; bonding to a fiberglass structure is an option. Thus, in many new boats, these shiny rods are exposed in the main saloon, but go unnoticed, allowing designers to meet an aesthetic challenge. The Bottom Line Modern engineering techniques and construction methods employed by major manufacturers, as well as marketing and legal concerns, are resulting in the production of better boats than at any time in the history of fiberglass, witness the number of American boats that meet ABYC and CE standards. In this environment, the odds of a structural failure are remote and, most likely, occasioned by a failure during the production cycle, or an inferior component. The rigging on these boats, however, is not to be neglected. As Brown explained of Roy Disney’s Santa Cruz 70 Pyewacket and her sisters, “those boats were well maintained and continually inspected. Losing a race as a result of mechanical failure was unusual.” Regardless of the age of a boat, annual inspection of standing rigging remains a must. In addition to inspecting wire for breaks, an owner should carefully examine the chainplate system from the point where it reaches the deck to its termination. Loose deck plates may result in water invading the hull or deck. Rust on the chainplate or bolts may indicate deck leaks, loose bolts or nuts producing a water leak or, in the worst case, the total destruction of the plate itself. Inspecting bolts and plates on a bulkhead is a simple matter; and removing cushions and furniture to allow inspection of the entire plate system is time well spent. A lesser effort might just invite major failure. RELATED ARTICLES MORE FROM AUTHORLeave a reply cancel reply. Log in to leave a comment Latest Videos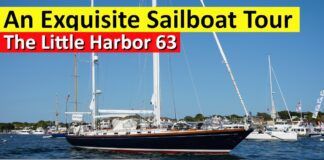 A Sailboat Tour of the Exquisite Little Harbor 63 Ketch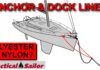 Dock and Anchor Lines – Polyester or Nylon?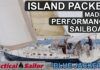 The Performance Sailboat from Island Packet: Blue Jacket 40 Boat Review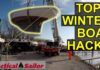 Top 3 Winter Boat HACKS!Latest sailboat review. 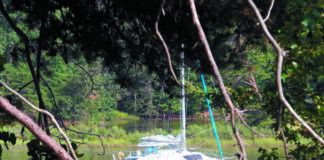 - Privacy Policy
- Do Not Sell My Personal Information
- Online Account Activation
- Privacy Manager
 - Forum Listing
- Marketplace
- Advanced Search
- About The Boat
- Gear & Maintenance
- SailNet is a forum community dedicated to Sailing enthusiasts. Come join the discussion about sailing, modifications, classifieds, troubleshooting, repairs, reviews, maintenance, and more!
Cost to Replace Chainplates? Should I Walk Away?I'm about to fly out to a pre-purchase survey on a 1985 Passport 40. I looked at a survey done on this boat last year and apparently the chainplates are original on this '85 boat. Noted was some water evidence near one of the port chainplates. I'll need to replace them regardless and would like to know what I'm in for cost-wise. I'll need to get some 316 SS water jet cut for the new chainplates and open up the interior to get the chainplates in. I'll likely do some of the work myself but may or may not depending on yard policies. Is this a $4,000 job or is it a $10,000+ job?? How much time would a yard take for this project? What would be a good yard for this in Washington? My intent is crossing oceans and voyaging for many years. I intend to own this boat for a long time. I'm experienced and have crossed oceans and I build/repair inspect aircraft for a living so not afraid of complex jobs. The survey indicates a newer Perkins installed in 2000 as well as several items I need such as wind vane and some newer sails and SSB and diesel cabin heat as well as some other recent upgrades. I realize I'll need to do a refit. I'm hoping not to do a massive years long refit turning into a money-suck. That would be dumb. If you've replaced your chainplates I'd be interested in how that went and it's cost. ...And if you know of anyone on the west US with a Passport 40 who might be willing to sell -I'm buying. Thanks in advance!  I don't think water jet is the best tool for cutting chainplates. It leaves a somewhat coarse edge that will need to be cleaned up to avoid corrosion. Personally I'd machine then (CNC or manual). There is no way that a few custom machined bars of 316 stainless steel should cost $10k. -Hmmmm. I thought water jet cut absolutely razor clean edges? Hence the reason for water jet cutting recommendations on chain plates. I know the need to polish and then electropolish to remove stress risers after the cutting. Is your comment that water jet leaves rough edges conjecture or first hand? Jus wonderin. Thanks.  One you would have to have really GOOD LUCK to find a boat with age X chainplates The cost is very much how hidden the plates are which can range from fully exposed and easy to remove to absolutely unable to even see them Making them again depends on what you are copying and there is nothing wrong with waterjet to make the shape it just a matter of to work necessary to finish the edges and bring the holes to final size compared to other methods As a point of reference (every boat and project is different), we replaced all of our chainplates with the rig up - 2 at a time. had new ones custom fabricated at a local shop. Did a great job! Total cost was under $400 for the fab work. We did all the installation labor ourselves. Well, refit is a relative word. I guess I meant offshore prep for safety. Refit seems to some to mean "replace everything". I think I used it incorrectly. Currently newer sails, refer, standing rigging instruments and engine indicate a concientious owner. I think a some of the people I see on the list are really brilliant with tools and then again some should not pick up a wrench. I see the same thing in aircraft -people buy an aircraft with starry eyes then realize they do not have the federal licence to perform the work. Parts are a fortune and so is my labor -but I'm good and very fair. The aircraft sits a long time and sucks money and tie down fees. So I think I know mostly what I'm in for. I'm intently avoiding a "project" boat. I'm attempting to take emotion out of the purchase equation but boats are alluring little beasties. I'd love to hear what someone who has done a chainplate r&r has to offer as advice on cost and time.  I have been working on aircraft and boats all my life and now I own a machine shop. working on aircraft in front of your shop is demanding work and some times hard because of the tight space requirements. but working on a boat that is in a yard or in the water can be much harder and way more time consuming then you would think. it is not as technical but a bit like working on a big jet on a muddy dirt strip and all you have is a latter and a crescent wrench. if you forget one tool you could be done for the day. its not the cost of the materials it is the labor from the yard that will put the job in the $6k range. no matter which way you choose to cut stainless you will need to finish the metal to a #7 finish ( mirror ) and passivate it if you want to prevent corrosion. water jet or Laser cut will give you just as good a finish as machining in which to start the sanding and polishing process and will cost a lot less. many boats have chainplates made of standard flat bar and only require being cut to length and drilled then polished. you can also buy flat bar that is already polished to a #7. a bit expensive but saves your on labor. if you think you will keep the boat more then ten years then go Titanium. expensive but no polishing is required to prevent corrosion.  Whats to prevent the OP from replacing the chain plates one at a time? Couldn't the work be done while the mast is still up, the boat is in the water and the yard doesn't have to know about it? That would save him thousands of dollars.  Chainplates are just one item. I'm not familiar with the PP 40 construction. What about the bulkheads they are attached to? If they need repair or replacement that adds additional time and expense. If the surveyor only noted one point of water intrusion, you might not have a major issue there. Worth a close look. As Tommays mentioned, how accessible the chainplates are will either complicate or simplify the task ? Then there's the standing rigging. But any vessel of that age is going to have needs of that nature that should be built in to the budget, unless they've already been addressed.  Bad chain plates and newer engine? Doesn't sound like a deal breaker to me. I think I've read that some people have moved chain plates to the outer hull.  Here is how to do this on a CSY 44 CLICKY NB Several CSY 44 owners have had chainplates fail.  Am replacing the chainplates on my boat- 8 in total. Cost Stainless metal (316) $25.00 each- cut to size, drilling the holes and welding spacers on the end. $0.00 - exchanged some wood work for the labor. Brought the stainless at http://www.pennstainless.com/ they will custom cut! Installing- about $30.00 for all new nuts and bolts, and another $40.00 for bedding material. Whatever you do DO NOT let the boatyard do this project, it's not a big deal, they wanted to charge me $200.00 per piece uninstalled.! Unless hey give you a reasonable price. But you will definitely save a lot of money by DYI. And I'm doing them 2x a time while the mast is up! no big deal here! Roland, Thanks for the support on this project!! You didn't mention the size of boat you did the work on but it sounds like you understand where I'm coming from. Liked that you noted the cost and suppliers. It's what I was hoping to hear. Now I just have to find somewhere to work on my boat if I go ahead with the purchase. I'm working on a 34 footer- finishing up somethings- in between the storms and then will start installing my chainplates. Where are you located? Nice boat! The Passport 40 Sailboat : Bluewaterboats.org group too! https://groups.google.com/forum/#!forum/PassportOwners  The only big expense in replacing chainplates is if they are inaccessible - glassed to the hull, hidden by elaborate cabinetry etc. or if their attaching points are rotted - bulkhead replacement needed and so forth. If it's simply replacing like with like it shouldn't even get to a boat buck - assuming you turn the wrenches. Take one or two out and give them to the machine shop to use as templates. They should be made from flat bar, not cut out of plate with a jet. Get them electropolished for a few bucks more and replace - then two more and so on. I did them on my Columbia 43, which included a fair bit of welding and the reconstruction of a fairly elaborate headstay fitting for less that $1K.  SloopJonB said: They should be made from flat bar, not cut out of plate with a jet. Click to expand... Now THAT is what I'm hoping for! $1000 bucks for parts and a #(*$&load of my labor should work ok. BUT, the surveyor noted that there was water intrusion in the port forward knee. Everything being equal I believe I may go ahead with the purchase simply because all the other things I'd need for an offshore boat are mostly there and fairly servieable/newer. I'll never find a 100% boat unless it's close to $200k and if I do the work I know it's solid. I would not go ahead with a boat that had a timed out engine unless it was completely compensated for in purchase price ie. appx. $18K.  Unless you simply like throwing away money I seriously suggest you give this man a call. He made my chain plates and another guys at my marina and they are WAY beefier than what I had and were almost too cheap to believe. Its high quality work but he charges extra for polishing, boring holes, ect ect. I just simply had the plates made and did the polishing and booring myself. I am not related to this man and have no continued working relation with him what so ever. Talon on this website also used him I believe after I gave him his info. Mr. James Idel. He works under the business Fab Solutions. His phone number is (904) 982-6113. Id give him a call- what could it hurt?  I live near Los Angeles but the boat is in state of WA. Intent -if I ok the purchase- is leave in WA for several mos. and purchase a WA cruising permit. Do a little work on and off. Sail south. Stop in Oregon for some days on way south and enjoy seafood. Pass Kalifornia completely without stopping ashore and go to a shipyard then marina in Ensenada for several mos. Return to CA after one year. I have retained a marine atty who is consulting me on this. You-know-why. Actually I would like to know why. Sales tax? What is a WA cruising permit. Well, my intent is serious voyaging so unfortunately I cannot trust any chainplates original to the boat. I'd be tickled pink to hear they had been replaced but it probably isn't so. Stainless is one metal that has a cumulative fatigue lifespan. Stainless work hardens. Work hardening means "brittle". A chainplate cycle loads and work hardens. I've heard of people removing their 'plates and breaking them in half with their hands. Easily. I did exactly that with my headstay fitting. It looked O/K but had some brown staining so I buffed it up with my buffing wheels. It came up like chrome but there was a faint hairline scratch remaining - I buffed some more but it was still there. I took the whole fitting in my hands and tried to bend it whereupon it twisted like taffy and snapped through the hairline mark. I doubt it took 20 lbs of force to tear it in two and it had looked perfect - the hairline was nearly invisible. At that point I pulled them all and made up new ones. Thank You! I have put his contact info in my file. I'll follow up after the survey... FYI, after my chainplates broke a couple years ago various riggers and other experts strongly advised using the new titanium alloy chainplates are the only way to go. Thanks. I have heard that titanium does not corrode (or takes forever). I may pursue that route but if the trade-off in dollars for titanium 'plates is insanely high I may stick with 316. I also like that Ti does not need polishing. That because I don't see the life of a 1985 boat being 60+ years. My knowledge of titanium is relative to aircraft. I gotta assume the really huge mass of titanium required to fab up 6 chainplates is outrageously expensive. Metals have recently gone sky high in price. One tiny 3/8 aircraft bolt in titanium costs about $12++. But I applaud you for having the foresight to install titanium and never have to worry again. That's peace of mind and worth the cost.  If your serious about going offshore then this project is a must and can be done by yourself. If your cruising plans are 10+ years and crossing several oceans then you will probably need to do the project again...probably in a little out of the way place with scant resources. I'm on my second set. DIY now, then you'll have the experience and knowledge to do it again. Titnium are a waste of money unless you are going to be keeping the boat for a very long time. Even thenbe why bother? You still onlyand have ten to fifteen years on the rigging. Its just another wy to spendthe more $ then youi need. Unless your circumnaving or sailing theis southern. Ocean beefy 316 will be justa fine. Id recomend titanium too if i was a seller. Motr $ in my poket.c This is what the person asking for advice stated: "My intent is crossing oceans and voyaging for many years. I intend to own this boat for a long time." So, with this in mind, you don't want to scrimp on chainplates.... go with Titanium. It is what you do in 2013 if you want the best. Top Contributors this Month 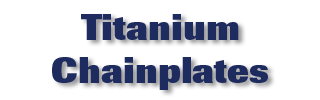 | | | Customer Service (302) 725-8300 | | | 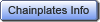 We will build titanium parts to your drawings. Just call Customer Service at (302) 725-8300 for a FREE quote.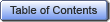 Description: | | Index: | | Normally Stocked? | | | In Stock? | | Alloy (Grade): | | Material: | | Measure: | | | For member pricing | Thickness: | | Use decimal format only. (i.e. 0.25) | Width: | | Use decimal format only. (i.e. 1.75) | Length: | | Use decimal format only. (i.e. 2.75) | Sub-Category: | | Please call (800) 725-8143 or (302) 249-3295 if you need help. The default quantity shown is the minimum order quantity. | | Item # Description | Group | Category / Sub Category | Price | | | Allied Titanium Stemplate for a Seaward 46, Grade 5 (Ti-6Al-4V) Titanium with Sandblasted Finish | | | Allied Titanium Upper and Lower Shroud Chainplate for a Seaward 46, Grade 5 (Ti-6Al-4V) Titanium with Sandblasted Finish | | | Screecher plate for tack of screecher sail on catamarran., Grade 5 (Ti-6Al-4V) Titanium with Polished Finish | | | Chainplate for Tayana 55 Sailboat, Grade 5 (Ti-6Al-4V) Titanium with Polished Finish | | | Custom chainplate for sailboat, Grade 5 (Ti-6Al-4V) Titanium with Polished Finish | | | Staysail Allied Titanium Chainplate for a 1981 Pearson 530 Cutter Ketch, Grade 5 (Ti-6Al-4V) Titanium with Polished Finish | | | Allied Titanium Stemplate for a 1981 Pearson 530 Cutter Ketch, Grade 5 (Ti-6Al-4V) Titanium with Polished Finish | | | Chainplate Cover for U-Bolt type Allied Titanium Chainplate on Hobie 33, 0.059 inches thick X 1-3/4 wide X 2-5/16 inch long with four holes for Item #0006179, Grade 2 (CP) Titanium with Sandblasted Finish | | | Custom Chainplate - First size (Enter dimensions in "cut size"), Grade 5 (Ti-6Al-4V) Titanium with Mill Finish | | | Custom Chainplate - Second size (Enter dimensions in "cut size"), Grade 5 (Ti-6Al-4V) Titanium with Mill Finish | | | Custom Chainplate - Third size (Enter dimensions in "cut size"), Grade 5 (Ti-6Al-4V) Titanium with Mill Finish | | | Custom Chainplate - Fourth size (Enter dimensions in "cut size"), Grade 5 (Ti-6Al-4V) Titanium with Mill Finish | | | Custom Chainplate - Fifth size (Enter dimensions in "cut size"), Grade 5 (Ti-6Al-4V) Titanium with Mill Finish | | | Custom Chainplate - Sixth size (Enter dimensions in "cut size"), Grade 5 (Ti-6Al-4V) Titanium with Mill Finish | | | Custom Chainplate - First size (Enter dimensions in "cut size"), Grade 2 (CP) Titanium with Mill Finish | | | Custom Chainplate - Second size (Enter dimensions in "cut size"), Grade 2 (CP) Titanium with Mill Finish | | | Custom Chainplate - Third size (Enter dimensions in "cut size"), Grade 2 (CP) Titanium with Mill Finish | | | Custom Chainplate - Fourth size (Enter dimensions in "cut size"), Grade 2 (CP) Titanium with Mill Finish | | | Custom Chainplate - Fifth size (Enter dimensions in "cut size"), Grade 2 (CP) Titanium with Mill Finish | | | Custom Chainplate - Sixth size (Enter dimensions in "cut size"), Grade 2 (CP) Titanium with Mill Finish | | | Stemplate for 1971 Islander 32 sailboat, Grade 5 (Ti-6Al-4V) Titanium with Polished Finish | | | Stemplate and double bow roller for Valiant 40, Grade 5 (Ti-6Al-4V) Titanium with Polished Finish | | | Port and Starboard Upper Chainplate for 1997 Tayana 52 Aft Cockpit Cutter Sailboat, Grade 5 (Ti-6Al-4V) Titanium with Polished Finish | | | Port and Starboard Forward and Aft Lower Chainplate for 1997 Tayana 52 Aft Cockpit Cutter Sailboat, Grade 5 (Ti-6Al-4V) Titanium with Polished Finish | | | Backstay Plate for 1997 Tayana 52 Aft Cockpit Cutter Sailboat, Grade 5 (Ti-6Al-4V) Titanium with Polished Finish | | | Port and Starboard Upper Chainplate for 1997 Tayana 52 Aft Cockpit Cutter Sailboat, Grade 2 (CP) Titanium with Polished Finish | | | Port and Starboard Forward and Aft Lower Chainplate for 1997 Tayana 52 Aft Cockpit Cutter Sailboat, Grade 2 (CP) Titanium with Polished Finish | | | Backstay Plate for 1997 Tayana 52 Aft Cockpit Cutter Sailboat, Grade 2 (CP) Titanium with Polished Finish | | | Mizzen Starboard Forward Lower Chainplates for a 1980 Vagabond 47 Cutter/Ketch, Grade 5 (Ti-6Al-4V) Titanium with Polished Finish | | | Chainplate for Upper Shrouds on a 1979 CSY 44 Walkover Cutter, Grade 5 (Ti-6Al-4V) Titanium with Sandblasted Finish | | | Chainplate for Fwd Lower Shrouds on a 1979 CSY 44 Walkover Cutter, Grade 5 (Ti-6Al-4V) Titanium with Sandblasted Finish | | | Chainplate for Aft Lower and Intermediate Shrouds on a 1979 CSY 44 Walkover Cutter, Grade 5 (Ti-6Al-4V) Titanium with Sandblasted Finish | | | Backstay Chainplates for a Valiant 40, Grade 5 (Ti-6Al-4V) Titanium with Polished Finish | | | Lower Shroud Chainplate for a Valiant 40, Grade 5 (Ti-6Al-4V) Titanium with Polished Finish | | | Upper Shroud Chainplate for a Valiant 40, Grade 5 (Ti-6Al-4V) Titanium with Polished Finish | | | Backstay Chainplates for a Valiant 40, Grade 2 (CP) Titanium with Polished Finish | | | Backstay Chainplates for a Valiant 40, Grade 2 (CP) Titanium with Sandblasted Finish | | | Backstay Chainplates for a Valiant 40, Grade 5 (Ti-6Al-4V) Titanium with Sandblasted Finish | | | Lower Shroud Chainplate for a Valiant 40, Grade 2 (CP) Titanium with Polished Finish | | | Lower Shroud Chainplate for a Valiant 40, Grade 2 (CP) Titanium with Sandblasted Finish | | | Lower Shroud Chainplate for a Valiant 40, Grade 5 (Ti-6Al-4V) Titanium with Sandblasted Finish | | | Staysail Chainplate for a Valiant 40, Grade 2 (CP) Titanium with Polished Finish | | | Staysail Chainplate for a Valiant 40, Grade 2 (CP) Titanium with Sandblasted Finish | | | Staysail Chainplate for a Valiant 40, Grade 5 (Ti-6Al-4V) Titanium with Sandblasted Finish | | | Upper Shroud Chainplate for a Valiant 40, Grade 2 (CP) Titanium with Polished Finish | | | Upper Shroud Chainplate for a Valiant 40, Grade 2 (CP) Titanium with Sandblasted Finish | | | Upper Shroud Chainplate for a Valiant 40, Grade 5 (Ti-6Al-4V) Titanium with Sandblasted Finish | 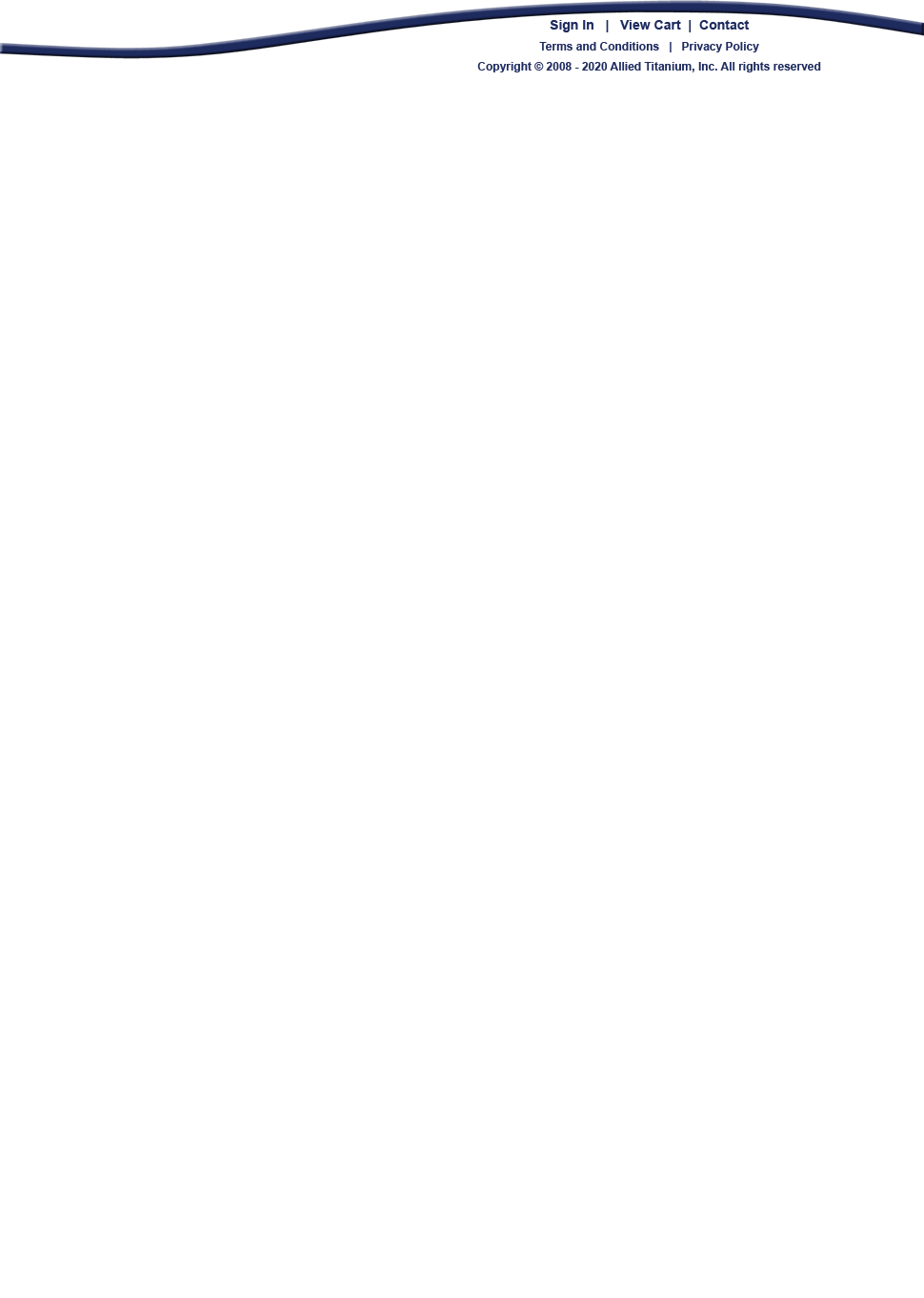 | (001) 401-739-1140 -- (001) 401-739-1149 | | | | These Chainplates are designed to be bolted directly to a flat Deck. Generally used for Shroud attachment on smaller boats, but sometimes used in Forestay and Backstay applications, they are suitable for larger boats and in other applications where the Deck is sufficiently reinforced.
Deck Mount Chainplates are listed below by the size of the Pin(s) they are attached to the rigging with. If you require Deck Mounted Chainplates not listed here, we stock some others and are able to fabricate a variety of Custom ones, please forward a sketch with complete measurements and details for a quote. (thru-Deck Mounted) . | | | Stainless Steel Deck Mount Chainplate with 3/16" Pin for attachment of Shroud. Formed SS Channel is attached to Deck with (2) 1/4" bolts on 1 5/8" centers. Unit is (maximum) 2" long x 5/8" wide x 3/4" high, Pin hole is 1/2" above deck. | | Stainless Steel Deck Mount Chainplate with Captive 3/16" Pin for attachment of Shroud. Captive spring-loaded Key Pin for quick release applications. Note that items attached to Key Pin require a (minimum) 1/4" hole. Formed SS Channel is attached to boat with (2) 1/4" bolts on 1 5/8" centers. Unit is (maximum) 2" long x 5/8" wide (excluding pin) x 3/4" high, Pin hole is 1/2" above deck. | | | | Stainless Steel Deck Mount Chainplate with 1/4" hole for attachment of Shroud. Welded SS Chainplate is attached to Deck with (2) 1/4" bolts on 1 1/4" centers. Unit is (maximum) 2" long x 1" wide x .100" thick, Pin hole is 1" above deck. Special replacement unit is 10% thicker than original as used on | | Cast Bronze Deck Mount Chainplate with 1/4" hole for attachment of Forestay or Backstay. Heavy-duty unit is attached to Deck with (4) 1/4" FH screws on 15/16" (forward) and 1 5/8" (aft) centers. Trapezoidal unit is (maximum) 2 1/4" long x 2 5/8" wide x 1 1/4" high, and 1/4" thick at the Pin hole. Pin hole is 3/4" above deck. for Backstay attachment. | | | Cast Bronze Deck Mount Chainplate with (2) 1/4" holes for attachment of Shrouds. Heavy-duty unit is attached to Deck with (2) 3/8" FH screws on 1 5/16" centers. Unit is (maximum) 2 3/8" long x 1 15/16" wide x 1 1/2" high, and 5/16" thick at the Pin holes. Pin holes are 1" above deck, and 13/16" apart.
| | | | Cast Bronze Deck Mount Chainplate with 5/16" hole for attachment of Shroud. Heavy-duty unit is attached to Deck with (2) 3/8" FH screws on 1 3/8" centers. Unit is 2 1/2" long x 1 3/4" wide x (maximum) 1 3/4" high, and 5/16" thick at the Pin hole. Pin hole is 1 1/8" above deck. | | | Cast Bronze Deck Mount Chainplate with (2) 5/16" holes for attachment of Shrouds. Heavy-duty unit is attached to Deck with (4) 5/16" FH screws on 3 3/4" (fore & aft) and 1 1/2" (side to side) centers. Diamond-shaped unit is (maximum) 4 5/8" long x 2 3/8" wide x 1 5/8" high, and 5/16" thick at the Pin holes, base is 1/4" thick. Pin holes are 1 1/8" above deck, and 1 1/4" apart. In addition to shrouds, this item is frequently used for attachment of a staysail stay, with the aft hole used for the tack of the sail. | | | Cast Bronze Deck Mount Chainplate with (3) 5/16" holes for attachment of Shrouds and Backstay. Heavy-duty unit is attached to boat with (5) 3/8" FH screws. Diamond-shaped unit is (maximum) 5" long x 4" wide x 1 5/8" high, and 3/8" thick at the Pin holes. Pin holes are 1 1/8" above deck. and others. Specify Port or Starboard. | | | | | Cast Bronze Deck Mount Chainplate with (1) 5/16" and (1) 3/8" hole for attachment of Shrouds. Heavy-duty unit is attached to Deck with (4) 5/16" FH screws on 3 3/4" (fore & aft) and 1 1/2" (side to side) centers. Diamond-shaped unit is (maximum) 4 5/8" long x 2 3/8" wide x 1 5/8" high, and 5/16" thick at the Pin holes, base is 1/4" thick. 5/16" Pin hole is 1 1/8" above deck, 3/8" Pin hole is 1" above deck. In addition to shrouds, this item is frequently used for attachment of a staysail stay, with the aft hole used for the tack of the sail. | | | | Stainless Steel Deck Mount Chainplate with 3/8" hole for attachment of Shroud. Investment Cast SS Chainplate is attached to Deck with (2) 5/16" FH screws on 1 3/8" centers. Diamond-shaped unit is (maximum) 2 7/16" long x 1 3/4" wide x 1 1/2" high, Pin hole is 1" above deck. | | Cast Bronze Deck Mount Chainplate with 3/8" hole for attachment of Shroud. Heavy-duty unit is attached to Deck with (2) 1/2" FH screws on 1 5/8" centers. Unit is 3 1/4" long x 2 11/16" wide x (maximum) 2" high, and 3/8" thick at the Pin hole. Pin hole is 1 1/4" above deck. | | | Cast Bronze Deck Mount Chainplate with (2) 3/8" holes for attachment of Shrouds. Heavy-duty unit is attached to Deck with (4) 5/16" FH screws on 3 3/4" (fore & aft) and 1 1/2" (side to side) centers. Diamond-shaped unit is (maximum) 4 5/8" long x 2 3/8" wide x 1 5/8" high, and 5/16" thick at the Pin holes, base is 1/4" thick. Pin holes are 1" above deck, and 1 1/4" apart. In addition to shrouds, this item is frequently used for attachment of a staysail stay, with the aft hole used for the tack of the sail. | | | | Cast Bronze Deck Mount Chainplate with 1/2" hole for attachment of Shroud. Heavy-duty unit is attached to Deck with (4) 3/8" FH screws on 2" centers. Unit is 3 1/4" square x (maximum) 2 1/8" high, and 9/16" thick at the Pin hole. Pin hole is 1 1/4" above deck. | | | | Cast Bronze Deck Mount Chainplate with 5/8" hole for attachment of Shroud. Heavy-duty unit is attached to Deck with (6) 1/2" FH screws. Unit is 4 1/2" long x 3 5/16" wide x (maximum) 3" high, and 5/8" thick at the Pin hole. Pin hole is 2 1/16" above deck. | | ~ Back to Chainplates Main Page ~ | | Join Duckworks Get free newsletter Comment on articles | Here an article how to make chain plates from carbon fiber and glass cloth. I was using these in a small way already for my own SC 435. Andrew dit not only made his stay connectors but also the cleats and rudder gudgeons in a similar way. Generally it is the way to go with materials we can get today - better load distribution, no corrosion, no leaking bolt holes etc. Here a link to a video I posted for Andrew. New materials give us possibilities to build better boats. Some of them you will never see on production boats. One of them is having chain plates for stays made from artificial material like uni directional carbon fiber and glass fiber. The advantage is an evenly distributed load on the hull. Chain plates on hulls impose stress points through the fasteners of the chain plate. So these areas must be beefed up with packing material. Over the years the bolts have the tendency to leak. Even when the chain plates are made from stainless steel and the fasteners are stainless steel bolts they can start to corrode. This is because the stainless steel in the bolts is a different material to the flat chainplate. Here a short description how to make 'organic' fastening points for stays. Start by fairing the area where the fastening point has to be build up. If necessary add fillets to smooth the area. Build up a distance piece from plywood. Prepare a short piece of PVC tube about 80 mm wide, diameter about 20mm to receive the stay. For small boats this can be a eyelet. Apply the first layer of uni directional carbon fiber. Fan these layers out as shown. The strands go from the outside to the inside in the same pattern and length. The u.d. strands have to be fanned out as shown. This way the load is distributed evenly over the hull. Next comes a layer of glass cloth. Generous overlap the U.D. strands inside and outside. The result is as I call it an "organic" boat. The load gets more evenly spread as with a connection with bolts - better stress relief and no chance of leaks through bolt holes. Website : www.ikarus342000.com 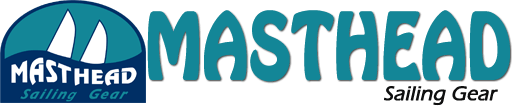 - Sail Accessories
- Storm Sails
- MARINE CLEARANCE
- Optiparts hardware & Opti Covers
- Sunfish Boat Covers and boat parts
- Laser Boat Covers and Boat Parts
- Other One Design Covers and Boat Parts
- 420 and FJ Boat Covers & Parts
- Catalina 310 & 320 Sails -New – In Stock
- Catalina Capri 22 Sails – Standard- In Stock
- Coronado 15 Sails – New
- Catalina 400 Sails – New
- Catalina 34 New Sails – In Stock – Standard and Tall Rig
- Catalina Wave Sail
- Catalina Capri 22 Sails -Tall Rig – In Stock
- Catalina 440, 470 and 50 Sails – New & Used
- New Catalina Furling Mainsails
- Catalina 387 – 380 – 390 New Sails
- Catalina Capri 26 and Catalina 27 – New Sails – In Stock
- Kayak Accessories
- Sailing Books
- GIFTS under $25
- Racing Gadgets
- Shackles & Snap Shackles
- Canvas Covers
- Dollies, Dolly Parts, Roof Racks
- Sailing Apparel and Gear
Come Visit Our New Location957 n. lime ave, sarasota, fl 34237, largest selection of used sails in the southeast, new custom sails * sail repairs * rigging * canvas, thousands of sails in stock. Masthead offers thousands of used sail choices; in stock at our location and ready to ship. All of our sails have been professionally evaluated by one of our sailmakers. Our sails come to you ready to use without the need for repairs. We offer modifications and alterations to match your requirements through our in-house, full service sail loft. To locate a sail on our website, go to our USED SAIL SEARCH TOOL CHOOSE a sail type and enter your approximate luff dimension in the search box: Don’t have your rig dimensions, no problem. Click here to search by boat: RIG DIMENSIONS TABLE . If you prefer for us to assist you in finding the right sail, please call 727-327-5361 or email: [email protected] OR fill out our contact form here and we’ll contact you: CONTACT FORM .  Used & ClearanceGet a great deal on new and used marine hardware and accessories. 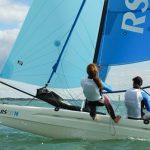 The RS Cat 16 XL is a class leading Roto-molded high performance beach cat with a modern hull shape. Can easily be single-handed or sail with a family crew. Exceptionally strong, simple and fast to assemble. Main and Jib standard with asymmetrical spinnaker and single trapeze. 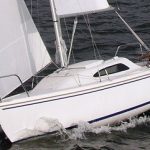 Catalina 22 Sport is our most popular boat. The Retractable Keel "swing keel" draws 1' 8" with the keel up and 5' with the keel down "It sails with the keel up or down". The new Catalina 22 Sport is the perfect west coast of Florida weekend cruiser or daysailor [..] 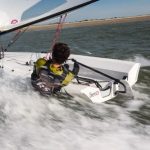 The RS Aero is a 21st Century modern single-handed sailboat, much like the Laser was 47 years ago. The Hull weighs 66 lbs. and total sailing weight at 88 lbs. RS's philosophy has always been to prioritize Ultra-Light weight, Performance and Practically in order to produce a simple, [...] Can’t find what you need, use our online contact form or call us Call: 727-327-5361 .  - Forums New posts Unanswered threads Register Top Posts Email
- What's new New posts New Posts (legacy) Latest activity New media
- Media New media New comments
- Boat Info Downloads Weekly Quiz Topic FAQ 10000boatnames.com
- Classifieds Sell Your Boat Used Gear for Sale
- Parts General Marine Parts Hunter Beneteau Catalina MacGregor Oday
- Help Terms of Use Monday Mail Subscribe Monday Mail Unsubscribe
Moving the chainplates to the Hull sides?- Thread starter Pilotocopilot
- Start date Feb 25, 2012
- Hunter Owner Forums
- The Cherubini Hunters
 PilotocopilotHas anyone done this on their 37C, I find it a pain getting around them and would seriously consider relocating them to the hull sides with backing plates through bolted on the inside. Any thoughts on disadvantages and advantages would be appreciated. I had toyed with that idea, as my boat dosent have proper chain plates, it has flat plates under the deck, onto which a right angle plate goes up through the deck, and the rigging attaches to this. I think it would be possible to put them onto the outside of the hull, but, i think their would need to be some form of re-enforcing, on the inside of the hull, like a strip of plywood, glassed in, because with how thin the fiberglass is on the hull, i dont think it would take long, for the bolts holding the chain plates, to elongate the holes, and then leaks. I decided not to do it, because of the chance of it leaking, and having to constantly be re sealed. But i would have to do it, to find out if that was really going to be the case. I consider chainplates that attach to the outside of the hull to provide greater integrity and strength to the rig and are highly desirable in a sea going vessel. The benefit of not having them obstruct the deck area are a secondary benefit.  Why Benny? Because the chainplates are stronger? Or does the increased angle of the shrouds strengthen the rig? Maybe one of our engineer members can do that math. If you move a shroud out six inches how does that change the loads? Use my boat: mast = 52.5' from keel, 45' from the partner; four lower shrouds = 23.3'; two uppers = 43.7'. Remember too that you have to change the angle of the spreader brackets.  Ed Schenck said: Why Benny? Because the chainplates are stronger? Or does the increased angle of the shrouds strengthen the rig? Maybe one of our engineer members can do that math. If you move a shroud out six inches how does that change the loads? Use my boat: mast = 52.5' from keel, 45' from the partner; four lower shrouds = 23.3'; two uppers = 43.7'. Remember too that you have to change the angle of the spreader brackets. Click to expand Would the hull need reinforcing at the attach point or is there enough hull thickness to support the tension. I have not had the opportunity to drill through the hull to have an idea of how thick the glass is from below the toe rail to let's say 20" down so I would appreciate any info on the hull thickness aspect as well. We've had to go around them every day for close to 10 months and I can say that you get used to them very quickly, so I would suggest taking some time before investing to much time and money in such a project. From a structural point of view, as said before, you'll need longer spreaders so that the lower section of the stays remain as parallel to the mast as possible. The spreaders may need to be beefed up to avoid buckling (this needs to be verified, as the section may already be overdesigned, as the rest of the boat). As for hull reinforcement, it would need to be investigated more deeply (hull thickness, lay direction...), but as always, if in doubt, and if it doesn't add a lot of weight/inconveniences, add material until you feel it's overdesign.  DianaOfBurlingtonI hear what your saying and coming from you I'll take it at face value, but boy are they a pain especially if your carrying anything. That's an interesting alternative I never considered. Do you see any issue then if the two lower shrouds were moved and not the upper. It may not be as big an issue going around one as it is all three, in addition not having to replace the spreaders circumvents having to drop the rig to make the changes. Don't worry nothing transpires until I sit and have a few drinks contemplating the changes and then maybe have a few more to make sure it's the right decision. I would move the upper alone without the lowers rather than the reverse. The upper benefits from the wider stance more than do the lowers. I am with you, Pilot, and find my best solutions occur after taking the time to contemplate each issue. Rarely do I get a purely-new 'Eureka' moment (though I had one today. I will post it to the blog when I finish what I started). Are you really in Lucaya? --or, where is the boat? I would consider having a look at it for you. The boat is just outside Lucaya one canal west of the Bell Channel, I'm up here in Toronto until the beginning of April then flying down for a month to renovate our condo down there. I will probably move it State side in June to somewhere in Florida - South Carolina,having no preference other than a cost effective place to haul out so I can do the bottom and have the transmission(slight leak in the rear seal) and prop shaft looked at ( may have worn out at the cutlass bearing). If you have the time John I'm always looking for crew to help with my trips, this one being about 3-5 days with the stream during some of the nicest sailing season for the area. I'm hoping to get a crew of 4 together,the boat has all the necessary safety equipment and then some, as it has to satisfy my wife, so from an EPIRB to Certified Life Raft to Sat Phone, Chart Plotter,Radar....... If your up to a little bit of offshore sailing. Gosh, after reading this I'm really going to have to consider moving the shrouds on my H30 to the toe rail. Having the deck clear to go forward would be really nice. The jib (150%) on my boat sheets outside the lifelines so there would not be any performance penalty. I'm going to have to replace the standing rigging on my boat soon anyway (the turnbuckles have run out of adjustment room) so that might be the time. I dont think you would need to change the spreaders, beacuase if you look up to your spreaders, the rigging goes straight up, it then curves at the spreaders, and goes to the masthead, if you moved it a few inches at the bottom, it would make no difference, i looked at mine, and its one side of the toe rail, as oppesed to the other side, it would make no difference to where the spreaders are. You have to remember this is not precission engineering, they invented all this years ago, where ropes and lines were all aproximate, and everything was expiremental. Nothing is exact on a sail boat, you can move lines and stays a few inches, with no effect, i am thinking of moving my main sheet, five feet forwards of where it is just now, and i know it will work better there, it will just get in the way more. Pilot, e-mail directly and know that I will definitely consider that trip! I'd be happy to look over the boat at any time if I can sort out how and when to get down there. AtlanticAl said: I dont think you would need to change the spreaders, beacuase if you look up to your spreaders, the rigging goes straight up, it then curves at the spreaders, and goes to the masthead, if you moved it a few inches at the bottom, it would make no difference, i looked at mine, and its one side of the toe rail, as oppesed to the other side, it would make no difference to where the spreaders are. You have to remember this is not precission engineering, they invented all this years ago, where ropes and lines were all aproximate, and everything was expiremental. Nothing is exact on a sail boat, you can move lines and stays a few inches, with no effect, i am thinking of moving my main sheet, five feet forwards of where it is just now, and i know it will work better there, it will just get in the way more. Click to expand I didnt say anthing about the 1970s, i was thinking more of the 1700s, when it was all expiremental, i think it still all experimental, and if you look at suhaili which was robin knox jonstones boat, it was built in india, by people who learned boat building from their fathers, and when they built it, they didnt know that it would be the first boat to sail non stop around the world, in the early photos, it dosent even have any spreaders, it was just built with basic tools, by indians who knew no maths or science, just basic boat building, yet that boat sailed round the world. I have also seen photos of my own boat, with the main sheet much further forward, right now, its five feet aft of the boom, but out of the way of everything, i want to move it forward, it would still be connected to the same place in the boom, but would just be directely below the place on the boom its connected to, it would just make the cockpit more clutered, and make the boat more awkward, if their is more than just me aboard, but i think for just me, it will make the whole rig easier to handle, as their will be less rope to heave in, and everything will be closer to hand.  DianaOfBurlington said: Yes, midboom sheeting is very popular; and I dislike it from a performance and engineering standpoint every time. It is merely a compromise imposed on boat buyers by the marketers for the sake of convenience-- all facts will support this. Midboom sheeting, on the average production yacht (Beneteau, Catalina, Hunter, et al) is definitely not a performance asset. Whether or not you would prefer it for your own boat, I respectfully advise you to know beforehand what the realities about it are, and then make your choice from a position of being informed. I hope you take this in the spirit intended. Click to expand  I've been following this thread, but have refrained from entering ... mainly because I didn't get it. We have one of the best sailboat designers of the time electing to place the shrouds/chainplate interface on each model where they are. And even today, boats are designed with a wide variation of chainplate placement. Why move them around unless one feels quite certain that a very noticeable improvement in performance will result? DianaofBurlington made this clear in his last post. As for easier walking along the deck, will moving the chainplates out really be than much of an improvement to compensate for the many hours and many $'s of expense. And to compensate for the violation of the original design? On my 1980 H36, yes I could move the shrouds out to the toe rail -- maybe 6-8". And yes that would allow more foot room on the deck. But still the angle of shrouds would require that the head/torso be bent inward anyway to pass by. No matter what, the deck will never be a jogging track. The only valid considerations should be will better performance and/or strength result? I've pondered many times the pros and cons of moving my shrouds inboard closer to the cabin top interface. For the reason DianaofBirlington cited. Less sheeting angle probably would allow better pointing. But moving the shrouds inboard would require real thought about how to insure strength integrity. Then one also also has to buy and install an inside jib track on the main deck next to the cabin top. Up to now, I sometimes use a reverse barber-hauler to pull the jib clew more to the center. This does pull the clew towards the center by up to a foot depending on wind velocity and the fore/aft location of the jib sheet snap blocks on the toe rail. But really I can't say for sure that I do much better on a close haul. My other tighter sheeting thought is to limit my jib size to say 95% so that I could lead the sheets inside the shrouds when close hauled. The smaller jib size would prevent the leach from rubbing up against and under the spreaders which was an issue when I experimented with my 135 Genoa (even furled a bit). When off the wind, the jib sheet would instead be led outside the shrouds for sheeting on the toe rails as John Cherubini designed. The attached pictures show the shroud into deck location on the 1980 Cherubini Hunter 36. Solid thick pieces of SS bar go through the deck and are very robustly tabbed to the hull. Its one very tough design. Attachments - This site uses cookies to help personalise content, tailor your experience and to keep you logged in if you register. By continuing to use this site, you are consenting to our use of cookies. Accept Learn more…
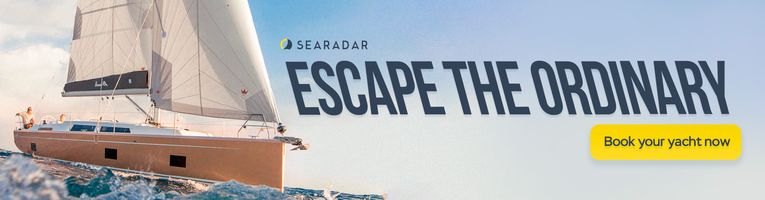 | | | | | | | | | | |
COMMENTS
Spars, Rigging, and Hardware for Sailboats. Rig-Rite, Inc. Phone: (001) 401-739-1140 -- FAX: (001) 401-739-1149 ... Chainplates and Stemhead Fittings are listed below by configuration, and then by the size of the Pin they are attached to the rigging with. ... we stock some others and are able to fabricate a variety of Custom ones, please ...
We can provide stainless steel chainplates and other parts that will last for years to come. (705) 725-1779 (800) 268-0395 Home; About; Products; Services; Boat Stairs. ... Whether you need multiple chainplates for your boat or you require a custom stainless steel product with unique specifications, our team can help you achieve your goals. ...
Sailboat manufactures mass produce their chainplates at the time of production, but older sailboats need to have custom made chainplates fabricated as they are no longer in stock. To manufacture your own chainplates, you need to locate the raw material: 316L Stainless Steel. 316L is readily available in various shapes and sizes, but for ...
Stainless Steel Chainplate Blank with 3/8" hole for attachment of Shroud. Chainplate Blank has no drilled holes for attachment to boat, and is designed for use in replacement applications where mounting bolt pattern varies, especially in older boats where Chainplates were hand drilled. Flat SS Chainplate is 10" long x 1 1/4" wide x 3/16" thick, 3/8" hole center is 3/4" from end.
Chainplates. At Mack Yacht Services, we know chainplates! In our experience, they are the most overlooked piece of equipment on boats today. Chain plates are the base of your rigging system and need attention just like everything else on your boat. Barring hurricanes, chainplate failure is the number one reason spars are replaced in our area.
You could cut the chainplates to length with a cutting wheel on a hand grinder then buff and polish as necessary. You'll need to either buy or borrow a drill press to drill the holes. ... and do it yourself for less than buying a set of chainplates and then you have the basic toolset for doing 99% of the custom metalwork on your boat ...
For safety and peace of mind, however, sailboat chainplates require attention and possibly upgrading. For example, many chainplates are too thin to grip clevis pins correctly. For a ½-inch turnbuckle with a ½-inch toggle, the chainplate should be at least ⅜ inch thick. For a ⅝-inch turnbuckle and toggle, a minimum thickness of.
Upper Shroud Chainplates C-30 Custom Pattern. Due to subtle changes during production, it is not possible to fabricate custom chainplates without having your old chainplate as an example. We both mechanically polish and then electropolish the completed chainplates. These steps are imperative to prevent immediate degradation of the assembly ...
The exact cost of replacing chainplates will vary by boat. An upgrade from stainless steel to titanium will increase the cost by 30 to 40 percent. For me, the sense of security my crew and I felt during our aforementioned 1,500-mile offshore journey was priceless. February 2020. know how diy maintenance. Everyone dreads the day that something ...
Home / Marine Products / Sailboat Hardware / Chainplates. Chainplates. Oneida offers both standard and custom sailboat hardware. Examples of our current offerings of chainplates include: Item #: 401369 CHAINPLATE, P&S PAIR, 316 S.S. Item #: 129-20-61-0001 STEM HEAD C-PLATE, POLISHED, 316 S.S.
Double Chainplate Set allows for attachment of (2) 3/8" Pins for Shrouds on each side of the boat. Chainplate Set is bolted through Bulkhead belowdecks with Backing Plate on other side of Bulkhead, using (8) 5/16" (8mm) bolts and locknuts, Cover Plate is attached to Deck. Stainless Steel Chainplate Set includes (2) Chainplates (CP 84-272-1), (2 ...
By The Rigging Company February 2, 2015. The chainplate is typically a metal plate used to fasten a stay to the boat. One end of the chainplate has a hole for the pin of the turnbuckle, the remainder of the chainplate is used to attach the plate to the boat via a bulkhead, knee, tie rod or the hull itself. Chainplates get their name from the ...
The quote I got from Atlas Bronze for 3/8" silicon bronze (C65500) plate dimensioned 24" x 16.75" (enough for all the chain plates and at least a few tangs) was $915. If I used all the material to make chainplates, that works out to about $114/ea. Aluminum bronze (954) cast bars 3/8" x 2" from Online Metals are $106/ea.
Chainplates on the 50-footer were installed using a method mirroring that of the J/133. Shrouds on cruising boats, however, may be located outboard at the rail, for instance, at the expense of tighter sheeting angles and greater pointing ability. And when located outboard, they may be buried behind cabinetry as an aesthetic consideration.
I'm bedding the new chainplates I bought from CD. I feel good about the steps I have taken so far. 1. Drill into existing 3/8" holes with the 1/2" bit. 2. Dremel out the accessible wooden core inside the perimeter of the 1/2" hole (even though it is still solid as can be). 3. Fill the gap from...
BluemanSailor. 87 posts · Joined 2009. #15 · Jun 28, 2013 (Edited) Am replacing the chainplates on my boat- 8 in total. Cost Stainless metal (316) $25.00 each- cut to size, drilling the holes and welding spacers on the end. $0.00 - exchanged some wood work for the labor.
Marine. Rigging Parts / Stemplate. 4,064.10. Each. Qty in Stock: 7. 0006185. Chainplate Cover for U-Bolt type Allied Titanium Chainplate on Hobie 33, 0.059 inches thick X 1-3/4 wide X 2-5/16 inch long with four holes for Item #0006179, Grade 2 (CP) Titanium with Sandblasted Finish.
Eventually I will make some changes to allow this to be bedded with butyl correctly. But that will involve removing the chainplate, converting the cover to through-bolted instead of wood screws. This will likely involve making a new cover that is a tighter fit. Ideally I would like to find a way to have the covers welded onto the chainplates.
Spars, Rigging, and Hardware for Sailboats. Rig-Rite, Inc. Phone: (001) 401-739-1140 ... Deck Mount Chainplates: Deck Mount Chainplates: These Chainplates are designed to be bolted directly to a flat Deck. Generally used for Shroud attachment on smaller boats, but sometimes used in Forestay and Backstay applications, they are suitable for ...
If necessary add fillets to smooth the area. Build up a distance piece from plywood. Prepare a short piece of PVC tube about 80 mm wide, diameter about 20mm to receive the stay. For small boats this can be a eyelet. Apply the first layer of uni directional carbon fiber. Fan these layers out as shown.
SPINNAKER. STORM SAILS. Don't have your rig dimensions, no problem. Click here to search by boat: RIG DIMENSIONS TABLE . If you prefer for us to assist you in finding the right sail, please call 727-327-5361 or email: [email protected]. OR fill out our contact form here and we'll contact you: CONTACT FORM.
Mar 2, 2012. #8. By moving the shrouds outboard, you limit your headsail sheeting options. Also, you will have the breach of hull integrity by fastening them to the hull. We built the first Cherubini 44 cutter for Warren Luhrs who wanted the chainplates bolted through the hull (probably for the reasons mentioned here).
Cayo Boatworks was born from our unwavering passion for shallow water fishing and our relentless pursuit of skiff perfection. We pour our hearts and expertise into every aspect of our craft, from conceiving original designs in-house to leveraging cutting-edge 3D computer-aided design technology. Our commitment to excellence extends to precision ...